Troubleshooting Your Equipment: When to Call for Packaging Machine Repair
Troubleshooting Your Equipment: When to Call for Packaging Machine Repair
Blog Article
Quick and Reliable Packaging Device Repair Service Services to Reduce Downtime
In the affordable landscape of manufacturing, the efficiency of product packaging procedures depends upon the dependability of machinery. Quick and trustworthy repair service services are essential in alleviating downtime, which can cause considerable functional setbacks and economic losses. Comprehending the importance of prompt treatments and the role of expert service technicians can change how businesses come close to upkeep and repair services. Browsing the myriad options readily available for repair service solutions can be challenging. What elements should organizations think about to ensure they are making the appropriate choice for their operational demands?
Value of Timely Repair Works
Timely repair services of product packaging machines are vital for maintaining operational performance and reducing downtime. In the fast-paced environment of manufacturing and packaging, even minor breakdowns can cause substantial delays and performance losses. Addressing issues promptly ensures that makers run at their optimal capability, thus safeguarding the flow of procedures.
Furthermore, normal and prompt maintenance can prevent the rise of small troubles into significant break downs, which often sustain greater fixing prices and longer downtimes. An aggressive technique to maker repair not just protects the stability of the equipment yet also enhances the general dependability of the manufacturing line.
In addition, prompt repair work contribute to the longevity of product packaging machinery. Machines that are serviced immediately are much less likely to deal with excessive wear and tear, permitting businesses to optimize their financial investments. This is especially crucial in markets where high-speed product packaging is essential, as the demand for consistent performance is paramount.
Benefits of Reliable Company
Reputable solution providers play a critical role in guaranteeing the smooth procedure of product packaging devices. Their competence not just boosts the effectiveness of fixings yet likewise adds significantly to the long life of equipment.
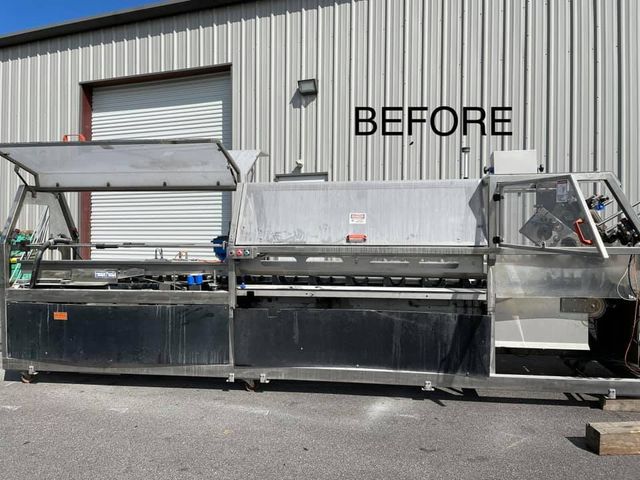
Additionally, a respectable solution copyright offers comprehensive support, including training and guidance for personnel on equipment procedure and upkeep ideal techniques. This not just empowers workers yet additionally grows a culture of safety and security and efficiency within the company. Overall, the advantages of involving trustworthy provider prolong beyond instant repairs, favorably impacting the whole functional operations of product packaging processes.
Common Product Packaging Equipment Problems
In the realm of product packaging procedures, various problems can compromise the efficiency and functionality of makers (packaging machine repair). Another usual problem is misalignment, which can trigger jams and uneven packaging, affecting item quality and throughput.
Electric issues view publisher site can likewise interrupt product packaging operations. Faulty wiring or malfunctioning sensors might result in erratic machine behavior, creating hold-ups and increased functional costs. In addition, software application problems can prevent the machine's shows, causing operational inefficiencies.
Inconsistent product flow is another essential issue. This can develop from variations in product shape, size, or weight, which may influence the machine's ability to deal with items precisely. Insufficient training of operators can worsen these issues, as inexperienced personnel might not recognize very early indicators of malfunction or might misuse the devices.
Resolving these usual packaging device problems quickly is important to preserving efficiency and making sure a smooth operation. Regular examinations and positive maintenance can dramatically reduce these problems, cultivating a trusted product packaging setting.
Tips for Decreasing Downtime
To minimize downtime in product packaging operations, carrying out a positive upkeep method is crucial. On a regular basis arranged upkeep checks can recognize potential issues prior to they rise, making certain devices operate effectively. Establishing a regimen browse around this web-site that includes lubrication, calibration, and inspection of vital components can substantially reduce the regularity of unforeseen breakdowns.
Educating team to operate machinery correctly and recognize very early warning indicators of breakdown can additionally play an essential role. Empowering drivers with the knowledge to perform basic troubleshooting can protect against minor concerns from creating significant delays. Moreover, keeping an efficient stock of vital extra components can accelerate repair services, as waiting for parts can bring about extensive downtime.
Furthermore, documenting equipment efficiency and maintenance tasks can help determine patterns and frequent troubles, permitting targeted treatments. Incorporating advanced monitoring modern technologies can provide real-time information, making it possible for anticipating maintenance and lessening the danger of abrupt failings.
Last but not least, cultivating open communication in between operators and upkeep groups makes sure that any type of abnormalities are without delay reported and dealt with. By taking these positive procedures, services can boost functional efficiency and dramatically lower downtime in packaging processes.
Picking the Right Repair Service Service
Picking the appropriate fixing service for packaging makers is an essential decision that can considerably affect operational performance. Begin by examining the supplier's experience with your details type of product packaging tools.
Following, consider the provider's credibility. Seeking responses from various other services within your industry can offer understandings into reliability and high quality. Accreditations and partnerships with recognized tools producers can also show a dedication to excellence.
In addition, assess their reaction time and availability. A provider who can provide punctual support decreases downtime and maintains production circulation steady. It's also crucial to ask about warranty and solution guarantees, which can show the self-confidence the company has in their work.
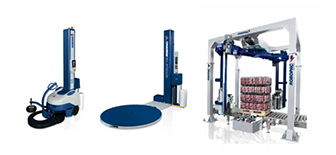
Verdict
Finally, the relevance of quick and reputable product packaging machine repair service services can not be overemphasized, as they play a critical duty in decreasing downtime and ensuring operational efficiency. By prioritizing timely fixings and selecting dependable company, companies can effectively maintain and address usual concerns productivity. Executing aggressive upkeep techniques and purchasing staff training further enhances the longevity of packaging machinery. Ultimately, a tactical technique to repair solutions promotes an extra resilient production setting.
Timely repairs of product packaging equipments are vital for maintaining operational Visit This Link effectiveness and minimizing downtime.Furthermore, timely repairs add to the longevity of product packaging equipment. Generally, the benefits of engaging reliable service carriers prolong beyond prompt repair services, positively impacting the whole functional workflow of product packaging processes.

Report this page